accelerators
Adhesive accelerators are specialized compounds designed to expedite the curing or hardening of adhesives. They work in synergy with adhesive formulations, catalyzing the cross-linking or polymerization reactions that result in a durable and robust bond. By significantly reducing the time required for adhesives to cure, these accelerators enhance production efficiency, decrease assembly line bottlenecks, and ultimately save valuable time and resources for manufacturers.
Adhesive accelerators offer a competitive edge by reducing bonding times and accelerating production cycles. By improving adhesive properties, accelerators help ensure that the final bonded product meets or exceeds the stringent requirements of diverse industries. Whether its automotive components subjected to extreme vibration and stress, or electronic devices operating in harsh conditions, adhesives fortified with accelerators provide the reliability and longevity needed for critical applications.
Another significant benefit of adhesive accelerators is their versatility. These additives can be customized to suit different adhesive formulations and substrates, making them adaptable to a wide range of bonding applications. Whether it's bonding metal to metal, plastic to plastic, or dissimilar materials together, adhesive accelerators can be tailored to optimize adhesion for specific combinations.
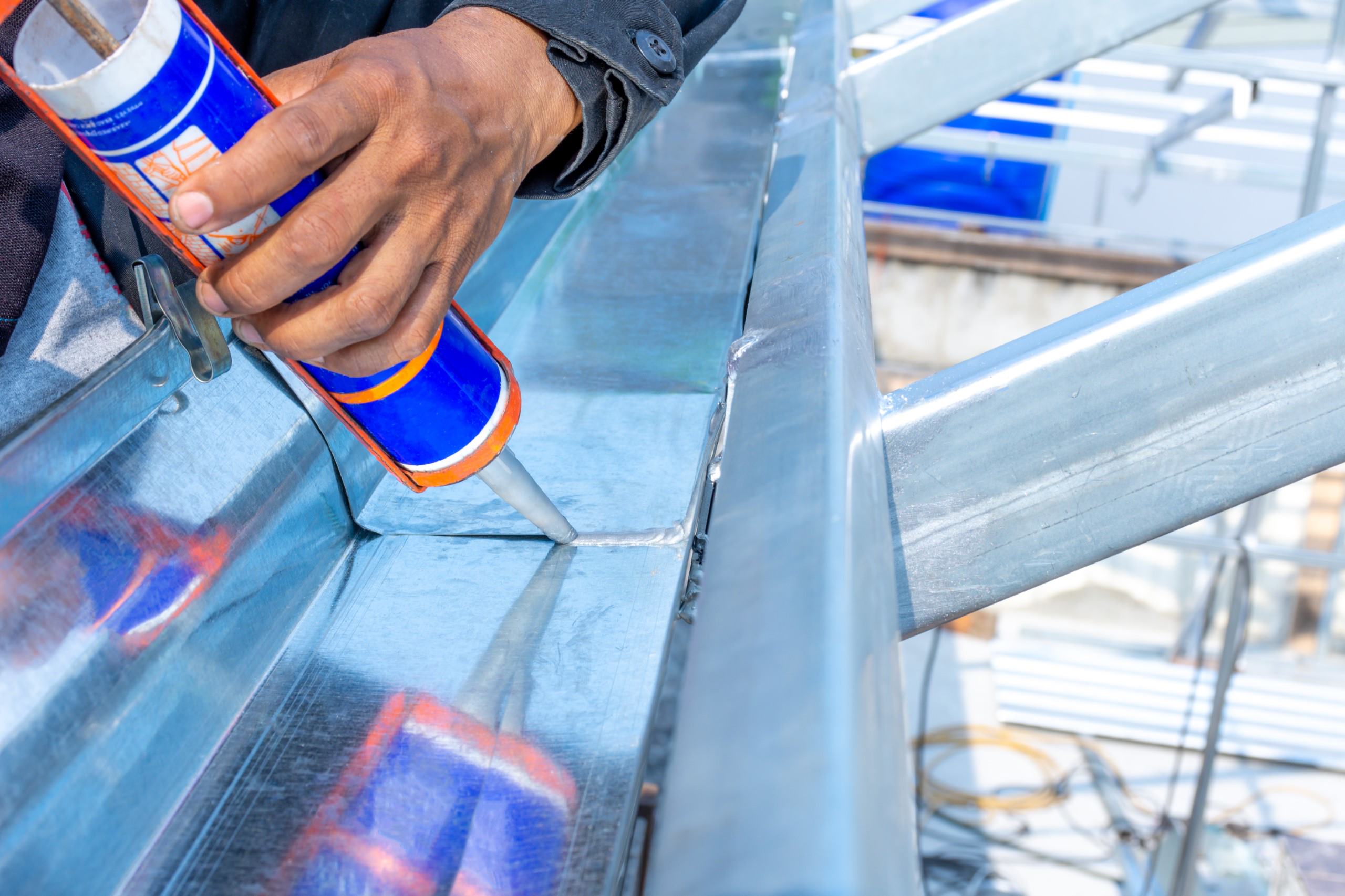
Reilly™ PDHP Adhesive Accelerator is largely used in second generation acrylic adhesives (SGA’s), also known as reactive acrylics or tough acrylics. Second generation acrylic adhesives are excellent at bonding unprepared or oily metals with fixture times of one to several minutes. They are exceptionally tough, with high impact and peel strengths. Reilly PDHP Adhesive Activator is a purified form containing over 80% of the active ingredient (dihydropyridine), which offers significant improvements in cure times and coloration versus other crude mixtures with lower purity.
Di-Pip™ Amine is used as a component of polyamide hot melt or custom blend adhesives. Due to their high heat and chemical resistance properties, polyamide-based hot melt adhesives are generally used in electronics, automotive, and aerospace applications. Di-Pip Amine bonds easily with different porous materials and imparts ultra-adhesive properties for high heat, high tensile environments.
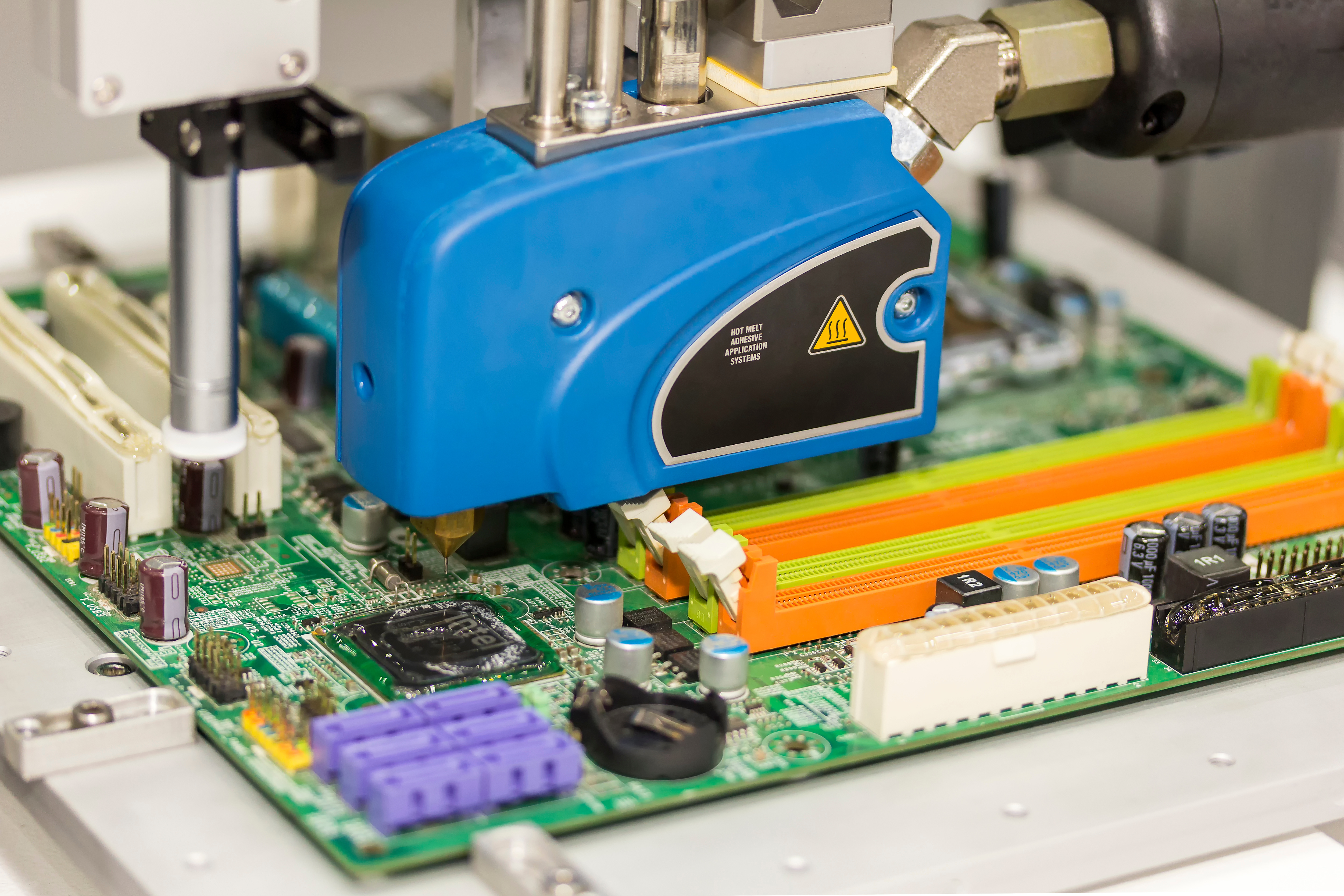